Mareterra Becomes Monaco's First Eco-district
Mareterra is Monaco's first certified eco-district. 85% of the coastal infrastructure was transported by sea...
A 6-hectare neighbourhood overlooking the sea: 60,000 m² of luxury housing and a new coastline stretching 1 kilometre ... in all a €2 billion project. Mareterra is taking the world by storm. The new district, developed by the Monegasque company (SAM) l'Anse du Portier with the help of others, notably the multinational construction giant Bouygues Travaux Publics, will comprise 10 luxury villas, four townhouses ranging in size from 600 - 2,000 m², plus 110 apartments. These exclusive properties with access to a seawater swimming pool named ‘The Princess Charlene Pool’ have already found purchasers at record prices. The Principality's eleventh district, designed by three megastars of eco-friendly modern architecture - Denis Valode, Michel Desvigne and Renzo Piano – will also house an extension to the Grimaldi Forum, a 3,000 m² shopping area and a wide seafront promenade. Not to mention an artificial wooded hill planted with 1,000 trees from a Tuscan plant nursery, a meditation room decorated by a Vietnamese artist, a blue grotto that allows visitors to see inside one of the concrete casings, and a mobile sculpture by Alexandre Calder, originally acquired by Princess Grace...
For this new extension into the sea, started in 2015, a site had to be created from scratch, surrounded by a protective belt made up of 18 reinforced concrete casings placed on an underwater embankment. This required 2.8 million tonnes of quarried materials for the landfill, the embankment and the ballasting of the blocks! At 26 metres high and weighing 10,000 tonnes each, the 18 reinforced concrete casings manufactured in Marseille were transported to Monaco one after the other. A journey of more than 200 km made with the help of a tugboat, which represented a real technological challenge.
Limiting the impact on the environment
For the project developers, the main issue was to find innovative solutions to limit the impact of this colossal construction site on the sea. 500 m² of Posidonia beds (the seaweed that serves as a nursery for fish) were moved and transplanted. ‘Mareterra was a real laboratory for research and monitoring; we only used the best practices. Posidonia has never been moved over such a large area anywhere in the world. The preservation of Posidonia has been a problem for a long time, particularly for industrial ports. Previous preservation methods did not work well. Today, not only has the transplantation been successful, but we can see that the plant is colonising new areas,’ says Guy-Thomas Levy-Soussan, Managing Director of L'Anse du Portier, the Monaco contractor for the project. ‘Mareterra is the first eco-district in Monaco to be certified (by HQE Sustainable Urban Planning). We completed the first stage of the studies, there were interim monitoring audits, and the certification will be awarded on completion. As soon as the first stone was laid, we set out to do things right. We were lucky enough to have the time and investors who were concerned about protecting the environment to have the resources to do things properly. This is in line with the Sovereign's desire to encourage urban development that is as sustainable as possible,’ explains Guy-Thomas Levy-Soussan, who points out that ’this is a first for the Principality. We didn't have the same environmental and energy knowledge when we built Fontvieille, which was designed before 1973.’ Times have changed... ‘It's clear that some of this urban development took place at a time when we didn't know, for example, what damage we were doing to the marine environment. When Fontvieille was built, and before that the Sporting and Portier landfills, nobody knew that hectares of Posidonia grass had been destroyed. No one was concerned. The builders of the Fontvieille land reclamation project gloriously demonstrated how they were going to throw pebbles into the sea, but certainly not how they were going to protect the seabed... It never crossed anyone's mind,’ admits Bernard Fautrier, who for 10 years was formerly Minister for Public Works and Social Affairs for the Government of Monaco.
‘We supply 80% of our street lighting with green electricity from the neighbourhood'.
The main emphasis for Mareterra has been energy transition. ‘Concrete is made on site, and over 85% of the water-based infrastructures were transported by sea to reduce CO2 emissions. We are also using more environmentally-friendly concrete. We recycle fly ash from blast furnaces,’ explains Guy-Thomas Levy-Soussan.
Another landmark measure: ‘We wanted to create our own thalassothermal loop as soon as the project was launched in 2015, to use energy from the sea to cool and heat the district. After detailed review, the chosen solution was to connect directly to the government's thalassothermal network at Larvotto,’ adds the Managing Director of Anse du Portier, who has opted for an energy mix. The developers have also financed the installation of photovoltaic panels on the Grimaldi Forum. Panels have likewise been installed on apartment blocks, water gardens and the lifts running from Place Gabriella to the Port. It is now the largest photovoltaic energy production plant in Monaco.
We cover 80% of street lighting with green electricity from the neighbourhood, and what is produced by the buildings is fed back into the grid,’ explains the developer, who says he considered all possible options for the land extension, including wave energy and the installation of electric batteries. ‘We studied a number of solutions and chose to use tried and tested technologies...’
*In an interview with Observateur de Monaco during celebrations to mark Rainier III's 100th anniversary.
The Renzo, the most complicated building to construct
It doesn't happen every day. While we're more used to hearing about delays in building projects, Mareterra will be delivered seven months ahead of schedule, despite the health crisis linked to the Covid 19 pandemic. The main reason for this early completion is a reorganisation of the schedule. We reorganised everything to make the sequence of work more appropriate. Not to mention the fact that we had the luck to work with 300 companies (representing nearly 4,000 people), all of whom were highly committed and motivated,' enthuses Guy-Thomas Levy-Soussan. The Renzo was undoubtedly the longest and most complicated building to construct, as its structure is supported by pylons. This building resembling a cruise ship is named after its designer and hails a technical feat. ‘The height of the columns was calculated to let us look out to sea from the crest, giving the impression of a “building that floats”, to use Renzo-Piano's words. The Renzo is aiming for a rating of 'Excellent' on the BREEAM Quality Mark.
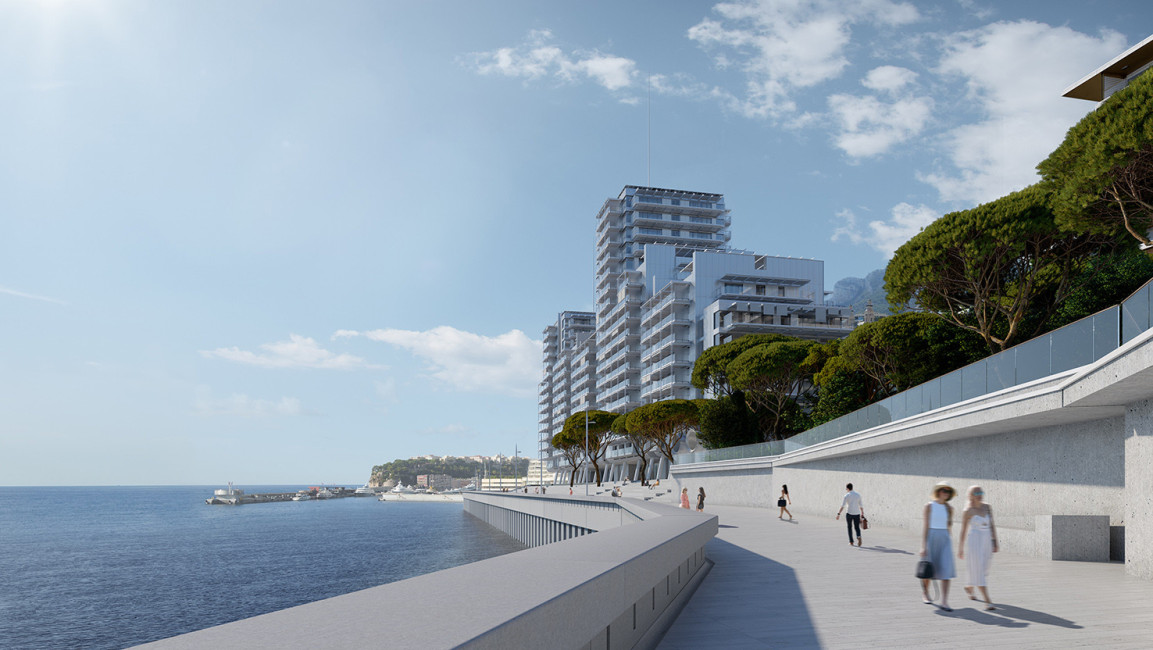
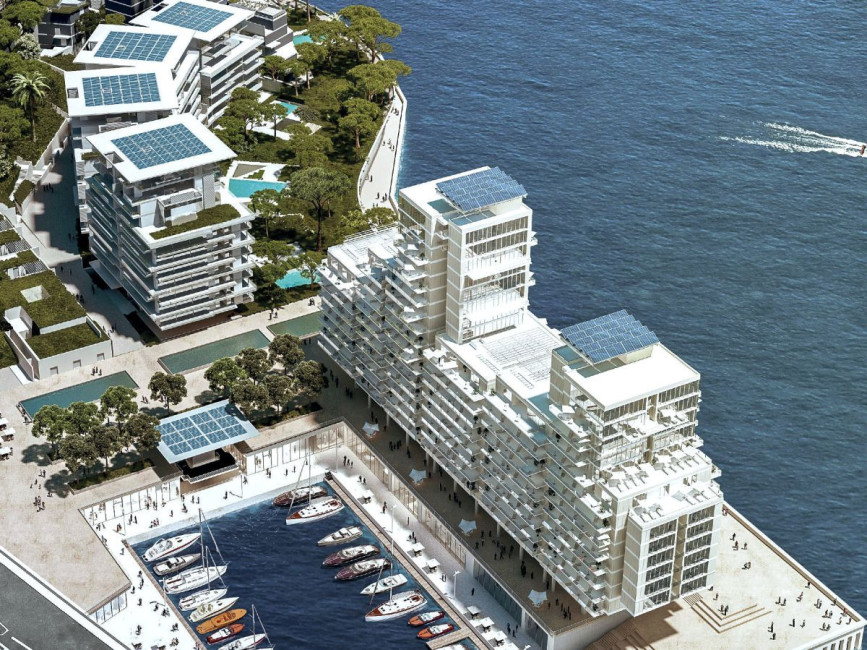